In the last ink-making post, I shared an experiment making carbon black ink – specifically with vine charcoal. The results were disappointing; the ink was pale, and struggled to flow evenly from a glass dip pen. This time I tried a couple different things. First, I doubled the amount of pigment in the ink, increasing it to two teaspoons of coarsely crushed charcoal, rather than one. Additionally, I varied the amount of water added in relation to the pigment and gum arabic, to see what sort of ratios would provide better flow characteristics.
Vine Black Ink, version 2.0
- 2 teaspoons vine charcoal, roughly crushed
- 7 milliliters liquid gum arabic (prepared previously)
- Up to 40 milliliters of water
The ink was prepared first by grinding the vine charcoal to a powder in a mortar and pestle. This yielded roughly one teaspoon of powdered pigment, which is closer to what I actually wanted last time. To this was added the liquid gum arabic, and the two were ground together for twenty minutes. At this point the ink formed a thick, black, undifferentiated syrup.
The first brush test was performed at this point. I think this would actually be a wonderful art ink. It is deeply black, and thick enough to generate interesting texture from a brush – the brushstroke frays apart rather than fading away.
An additional ten milliliters of water were added, and the ink was re-mixed. The second brush test was performed at this point. This is a pretty successful concentration of pigment (roughly 2 teaspoons of coarse pigment for a half ounce of ink). The ink here is still black, though not quite as opaque as in the first test. It still flows unevenly from a pen.
An additional fifteen milliliters of water were added (bringing the total to twenty-five). The third brush test was performed at this point. Here the ink is noticeably more translucent, more gray than black. It also flows markedly better from a glass dip pen. Most of the writing sample was performed at this point.
Finally, an additional fifteen milliliters of water were added (bringing the total to forty). No brush test was performed at this point, but some writing was done both with a glass dip pen and with a feather quill pen. The flow at this point was even smoother. The quill pen is harder to work with, as it wants to flow much more quickly, but the resulting writing is correspondingly more deeply black.
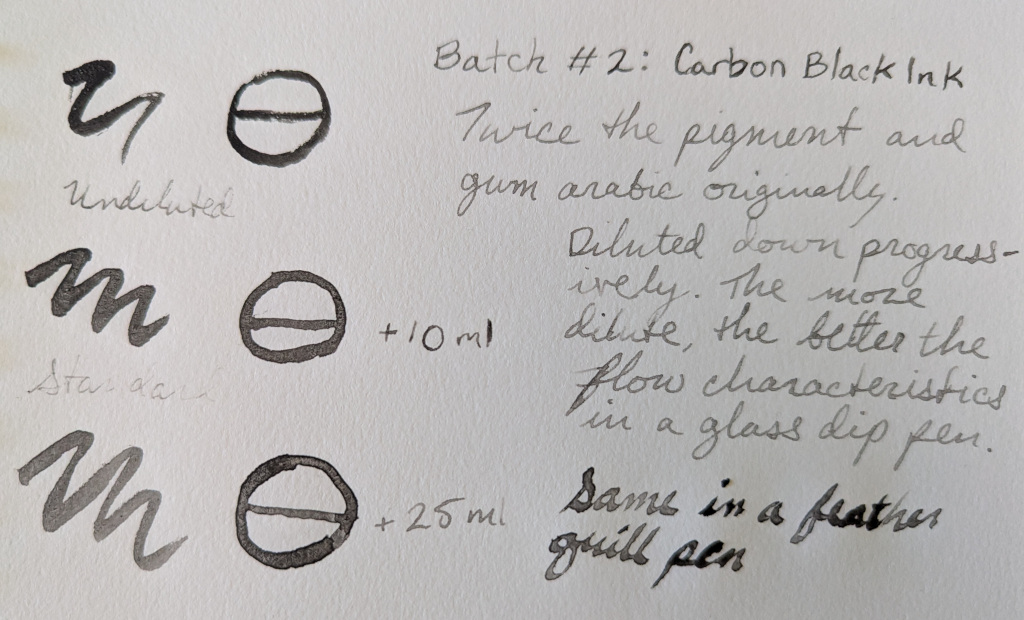
Learnings
Two teaspoons of coarsely crushed pigment – roughly one teaspoon once finely powdered – in a half ounce of ink is a much better concentration for Type I inks. That should be the new standard.
From a flow perspective in a glass dip pen, the less gum arabic I can get away with, the better. I knew this was true of fountain pens, but didn’t realize it held for a glass dip pen as well. By the end I was at about 2.7 milliliters of gum arabic to a half ounce of ink, and could have comfortably gone even lower.
This creates an interesting dilemma with Type I inks, in that you need enough binder to keep the pigment in suspension, but not so much as to inhibit smooth flow. The additional grinding time might help with this, but further experimentation is needed.
Leave a Reply